Vertex(バーテックス)
Vertexの特長
「頂点」を目指す、新しいコンセプトの5軸立形マシニングセンタ
横形トラニオンタイプの5軸マシニングセンタでトップクラスのシェアをもつ三井精機から、新たなコンセプトを持つ5軸立形マシニングセンタが誕生しました。
その名はVertex550-5X。“Vertex(バーテックス)”とは『頂点』『頂上』という意味を持ちます。コンパクトなボディに高性能な機能を凝縮しています。
Vertex550-5Xは従来近づき難かった5軸機のイメージを覆し、3軸機の延長線上として使っていただけることを目指しました。Vertexは5軸機をさらに身近にします。
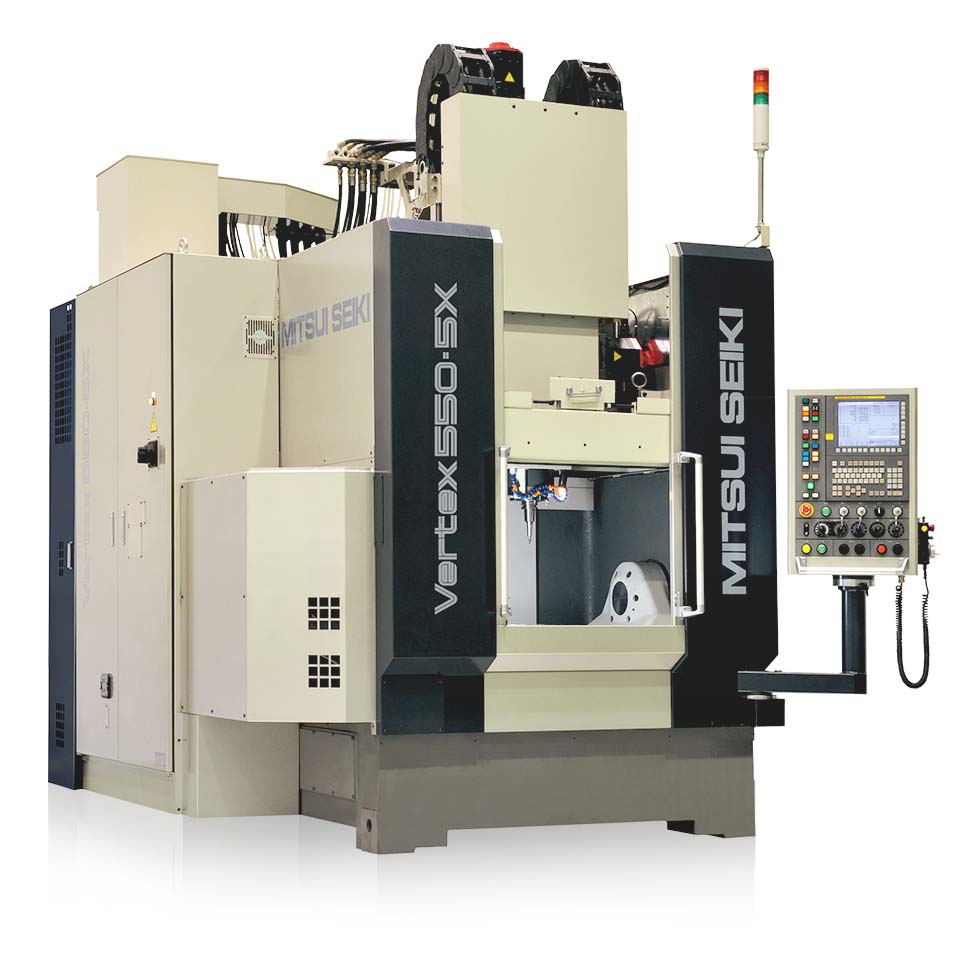
最小の設置スペースで最大の加工エリアを実現
Vertex550-5Xの設置スペースは幅2m×奥行き3m(標準仕様・操作盤含まず)です。このコンパクトなボディにもかかわらず、最大φ500mm×高さ325mm*のワークが積載可能です。
*最大工具長さ・径に制限が出ます。
*積載質量・モーメントに制限されます。
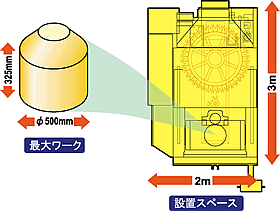
徹底的なつくり込みがもたらす高精度
Vertexの基本は高精度にあります。徹底したつくり込みによってジグボーラー並みの幾何学的精度を達成しています。また直線軸にはリニアスケール、回転軸にはロータリーインダクトシンを標準装備。位置決め精度の規格値をはるかに下回る実力があります。
Vertexは以上のような高精度と最小指令単位・移動単位0.1μmが融合し、ミクロン台の加工を実現します。
位置決め精度の実測例(X,Y,Z軸)
*参考データであり、保証値ではありません。
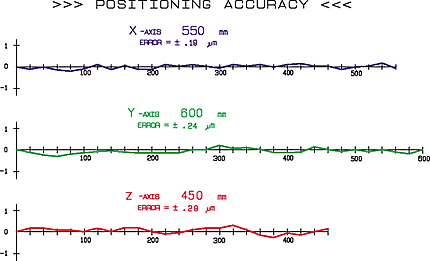
高速性能と高精度を両立した傾斜円テーブル
5軸機の要である自社製の傾斜円テーブルには、多くの出荷実績を持つ横形トラニオンタイプ5軸マシニングセンタの経験が生かされています。
A軸とC軸は特殊ギア駆動を採用。早送り、最大切削送り共、 A軸:30回転、 C軸:50回転を実現しました。また、ロータリーインダクトシンによるフルクローズドループを標準採用し、割出し精度A軸:±6秒、C軸:±4秒という高精度を誇ります。
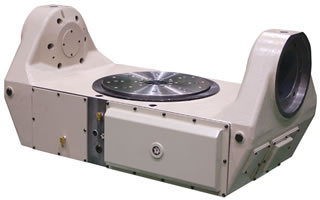
良好な切粉処理
従来、立形マシニングセンタの問題点であった切粉処理性能の低さをキューブオン構造が解決しました。
切削点で発生した切粉はテーブル直下に設置されたチップコンベア上に落下します。このコンベアにより切粉は速やかに機械後方の機外へ排出されます。
また、ベッドからの切粉排出口は後方の他に左右側面にも設置しました。柔軟なタンクレイアウトが可能です。
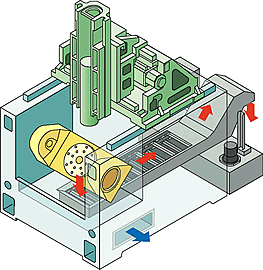
操作性を追及したデザイン
テーブル側が移動しないため、機械前面からテーブル中心までは(テーブル水平時)常に約400mmで極めて接近性が良好です。また床面からテーブル上面まで900mmは腰の位置と同じであり、またベッド下につま先が入るスペースがあるため、無理のない姿勢で作業ができます。
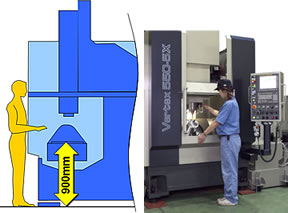
高速タイプと高トルクタイプ ― 選べるスピンドル
Vertexのために新規開発したスピンドルは2種類。高速タイプの25,000min-1と高トルクタイプの15,000min-1で、加工目的に応じてどちらも標準で選択できます。
またテーパーは標準の40Tの他にオプションでHSK-A63も対応可能です。
【主軸熱変位補正を標準装備】
主軸先端部にセンサーを設け、ここで検出した主軸熱変位量をリアルタイムでフィードバックし補正を行います。
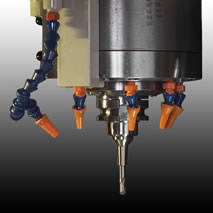
5軸加工の効果〈1〉
同時5軸制御によるインペラーの高能率加工
インペラー、ブリスク、タービンブレードなどは同時5軸制御でなければ加工できない部品です。
Vertexはプログラムで指令された複雑で高速な動きにも充分追従し、なおかつ従来のBT40クラスの切削能力をはるかに超えた加工能力を発揮します。
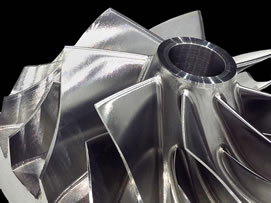
多面割り出しによる工程集約加工
多くの部品は複数の面に加工箇所が存在します。3軸機ではその都度段取り替えを行って加工しなければなりません。5軸機なら直線3軸に加えて傾斜・回転2軸を割出すことができます。そのため、
- 取付け面以外の面の全加工
- 段取り工数の大幅な削減
- 治具の簡素化、不要化
- 加工精度の向上
が可能です。
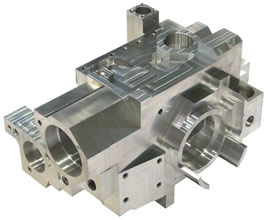
5軸工具先端点制御による加工
同時5軸制御加工において、ポストプロセッサ側では機械の傾斜軸・回転軸中心のずれ量を考慮してカッターパスを出力します。しかし、中心のずれ量は機械ごとに違うため、機械が変われば加工プログラムを作り直さなくてはなりません。
この機能は、パラメータに加工する機械固有の傾斜軸・回転軸中心のずれ量を入力しておけばNC側で計算を行うため、プログラム側で考慮する必要はありません。つまり、機械が変わっても同一のプログラムが使用でき、使い勝手が良くなります。
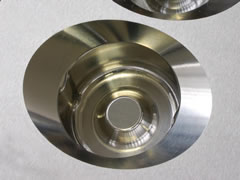
金型加工の5軸使用例1(割出し2軸+同時3軸によるコアの加工)
金型加工の分野でも5軸加工が注目され始めてきました。そのメリットは以下の通りです。
- 最適な方向から工具のアプローチが可能
従来放電加工機でしか加工できなかった金型が切削で加工可能に - 段取り替えが必要なワークでもワンチャッキングで加工が可能
金型製作時間(リードタイム)の短縮
省人化、無人化 - 加工時間の短縮、加工面品位が向上
従来ボールエンドミルを使用していた部分にフラットエンドミル等を使用できることで荒加工の取り代を多くできる
ギアケース・コア モデル加工の例
ワーク名称 | ギアケース・コア モデル |
---|---|
素材の寸法 | 260mm×220mm×高さ185mm |
材質 | NAK80 |
CAM | tools MX(グラフィックプロダクツ) |
協力 | 株式会社グラフィックプロダクツ |
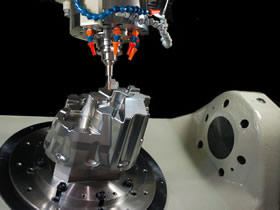
ギアケース・コアの加工を例に5軸加工のメリットを説明します。従来、このような金型の加工は電極を製作してから放電加工でしか方法がありませんでした。5軸加工のおかげで切削加工可能となり、金型製作のリードタイムを大幅に短縮できます。
A:立ち壁の高さは150mm以上あり、3軸機での上面方向からの加工はできません。
B:5軸機では、傾斜軸を90°割出した状態で回転軸を割出すことにより短い工具で加工が可能です。但し回転軸の割出し精度が悪いと壁のつなぎ目で段差が目立ちます。Vertexの高精度なテーブル割出しはこのような問題を解決します。
C:コーナー部分の加工はR1等の小径ボールエンドミルを使用しますが、このC部は高い壁が邪魔してやはり上面方向からの加工ができません。5軸機では傾斜・回転軸を割出して最適な方向から工具をアプローチさせることで加工可能となります。
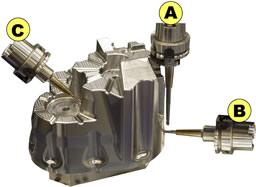
5軸加工の効果
3軸加工では電極を作成し、放電加工を行う工程は不可避でした。工程間の待ち時間など、実加工以外のアイドルタイムも発生し、本金型加工のリードタイムは130時間かかっていました。それを5軸化することにより電極作成時間の削減、工程間の待ち時間の解消等でわずか30.5時間に削減できました。
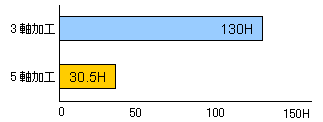
5軸加工の効果〈2〉
金型加工の5軸使用例2(同時5軸による加工)
加工データ
ワーク名称 | ギアケース・コア モデル |
---|---|
素材の寸法 | 260mm×220mm×高さ185mm |
材質 | NAK55 |
加工方法 | 軸工具先端点制御 |
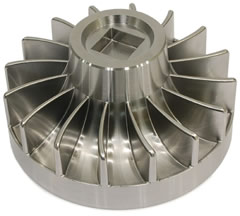
同時5軸加工の効果1…ポケット部の加工
テキストなし?テキストなし?テキストなし?テキストなし?テキストなし?
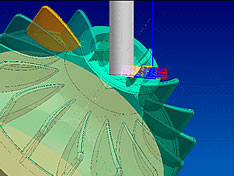
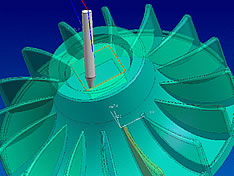
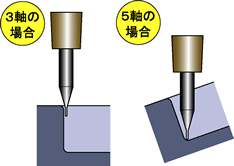
荒加工に径の太いフラットエンドミルが使える
→(1)切削性が良い(2)切粉の排出性が良い → 加工時間の短縮
ポケット仕上にR0.5ボールエンドミルが使える
→側壁と底面のつなぎ部分のコーナーが小さくても1本の工具で加工可能
同時5軸加工の効果2…フィン部・ハブ部の加工
テキストなし?テキストなし?テキストなし?テキストなし?テキストなし?
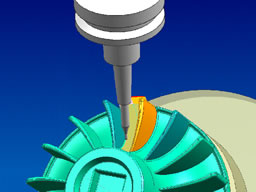
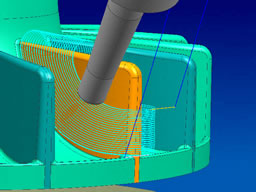
ハブの形状に沿って同時5軸で工具を動かす
- 荒加工で均一な取り代となるため、後工程の負荷が軽減される → 加工時間の短縮
- フィン部分とハブ部分のつなぎ目がきれいに仕上がる → 加工面品位の向上・磨き工数の低減
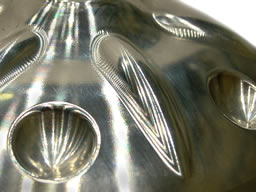
等高線加工や走査線加工で
つなぎ目部分に縞模様が目立つ
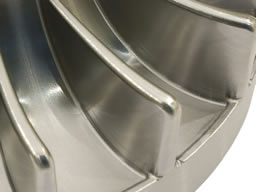
つなぎ目が目立たない
日本力(にっぽんぶらんど)賞 受賞!
5軸制御立形マシニングセンタ Vertex550-5X
第36回機械工業デザイン賞 日本力(にっぽんぶらんど)賞 受賞!
5軸制御立形マシニングセンタ Vertex550-5X が第36回機械工業デザイン賞 日本力(にっぽんぶらんど)賞を受賞しました。
機械工業デザイン賞は日刊工業新聞社が経済産業省の後援、日本商工会議所、各工業団体の協賛を得て、わが国工業製品のデザインの振興・発展を目的に1970年制定されました。
弊社は過去にVR3Aで通産大臣賞(当時)を受賞した他、VR5A、ねじ研削盤でも受賞しています。今回の受賞はVR3A以降約20年ぶりとなる快挙です。
本賞はデザインを基本にしていますが、性能、機能性、安全性、操作性、経済性、市場性などのあらゆる角度から対象製品が審査され、優秀と認められたものだけに贈られます。
本機は「ともすれば機能品質一辺倒になりがちな工作機械において、本製品は感性品質の次元に一歩踏み込んだ工作機械として位置づけることができる。」という高い評価を頂きました。
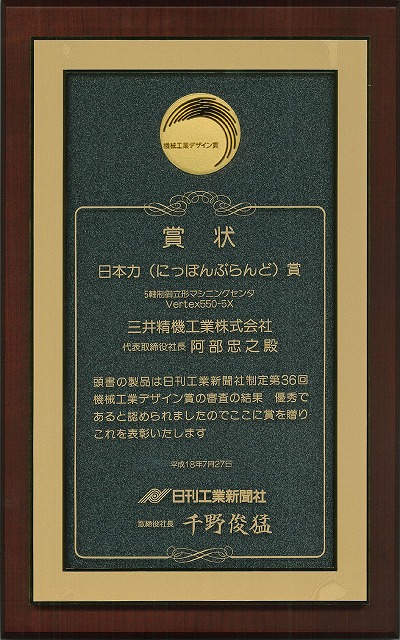
7月27日 機械工業デザイン賞 贈賞式
ホテル・グランドパレス(東京 飯田橋)にて
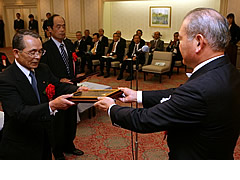
表彰される阿部社長
(写真提供:日刊工業新聞社)
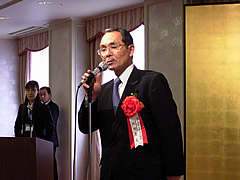
阿部社長の挨拶
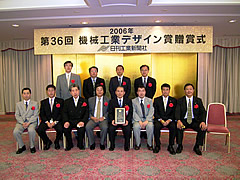