三井精機のモノづくり
「きさげ」のお話〈1〉
「きさげ」とは?
ノミ状の工具(「スクレーパ」「きさげ」と言います)を使用して鋳物の表面を削り取っていく作業です。
きさげ加工を行う場所は摺動面(テーブルやコラムなどが移動する部分)、物と物が接触する面、テーブル・パレットなどです。きさげによって一度に削り取れる量は1~3μm程度であり、除去量さえわかれば正確に自由な形状をつくっていくことができます。熟練者によるきさげ加工は、機械加工では得られない平面度、直角度、真直度を実現することができます。
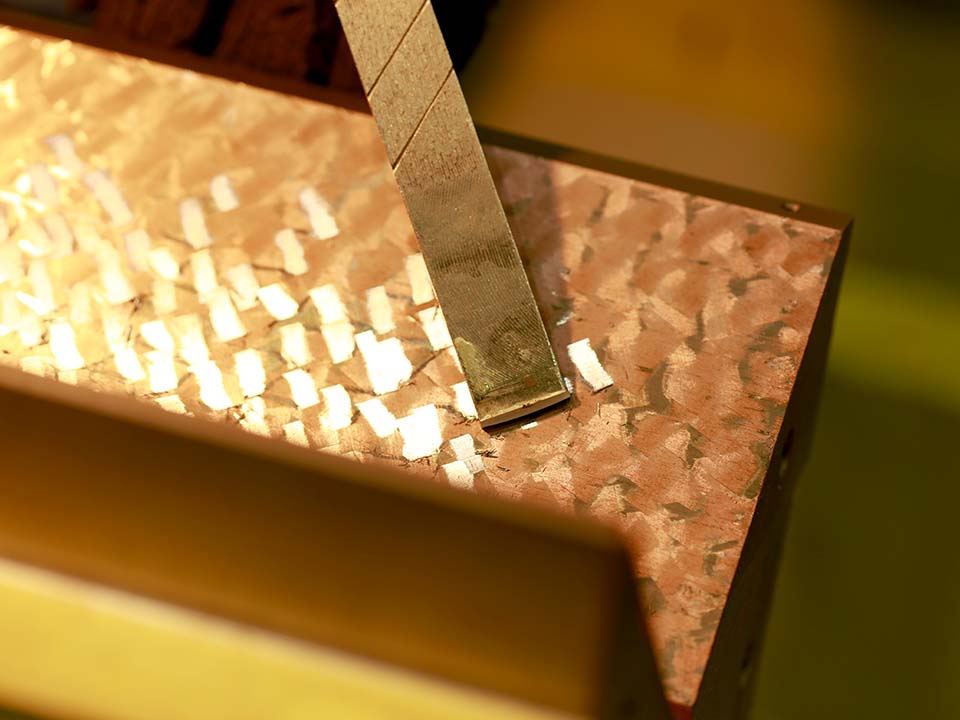
なぜ「きさげ」が必要なのか?
――それは簡単に言えば「親よりも良い子供はできない」ということです。
たとえば加工機で出せる平面度が10μmとすると、それで加工したものは10μmよりも良い精度が出ません。親よりも良い子供にはならないのです。それでは親よりも良い子供にするにはどうするか?(5μmの平面度を出すためにはどうするか?) ・・・ それは「矯正(教育)して良い子にする」ということです。つまり、きさげという人間による矯正手段を通して親の精度よりも良い子供ができるというわけです。
三井精機のモノづくりの基本はこの理念に基づいています。
「きさげ」の工程
きさげで正確な面を出そうとした場合、何か基準になるものが必要になってきます。それが、次に述べる「三面摺り」によってつくられた平面のプレートで、「摺り合わせ治具」と呼ばれています。
きさげをかけた面は微小な凹凸となっており、高い部分・低い部分があります。加工した面に朱を塗り、摺り合わせ治具と摺り合わせます。すると、高くなっている面部分の朱がはがれます。朱がはがれた部分を再度きさげし、これを繰り返していくことで平面が作られていくのです。
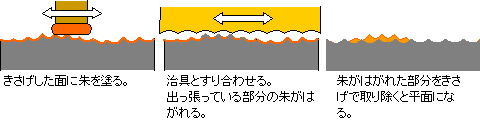
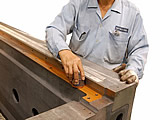
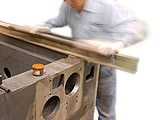
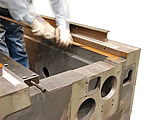
どのようにして平面を出すのか? ~三面摺りについて~
平面をつくることは、きさげの基本です。それでは、きさげによってどのようにして平面をつくるのかを「三面摺り」という方法によって説明します。
「三面摺り」と呼ぶからには、当然3つの面をつくるということです。では、なぜ3面なのでしょうか?
たとえば【図1】のような形の3つの平面をきさげでつくったとします。
【図2】のように3枚のプレートをそれぞれ違う組み合わせで摺り合わせます。ここでも先ほど述べた「摺り合わせ」の方法を使います。①と②、②と③はそれぞれの面がぴったり合います。しかし、この例の場合はたまたま2つの組み合わせがうまくいきましたが、2枚だけ面が合うことを確認しても平面とは言えません。それは①と③はぴったり合わないからです。

【図3】のように3つのプレートが平面になっていれば、【図4】のようにどの組み合わせでも面はぴったりと合います。つまり、3つのプレートがどのような組み合わせでも面が合う条件というのは平面しかないのです。三面摺りは、3枚のプレートをそれぞれ摺り合わせながら正確な平面をつくっていく作業です。

「きさげ」のお話〈2〉
「きさげ」を行う目的
三井精機では機械のさまざまな部分にきさげ加工を施しています。もちろん高い精度を出すためですが、部分によって目的が異なります。
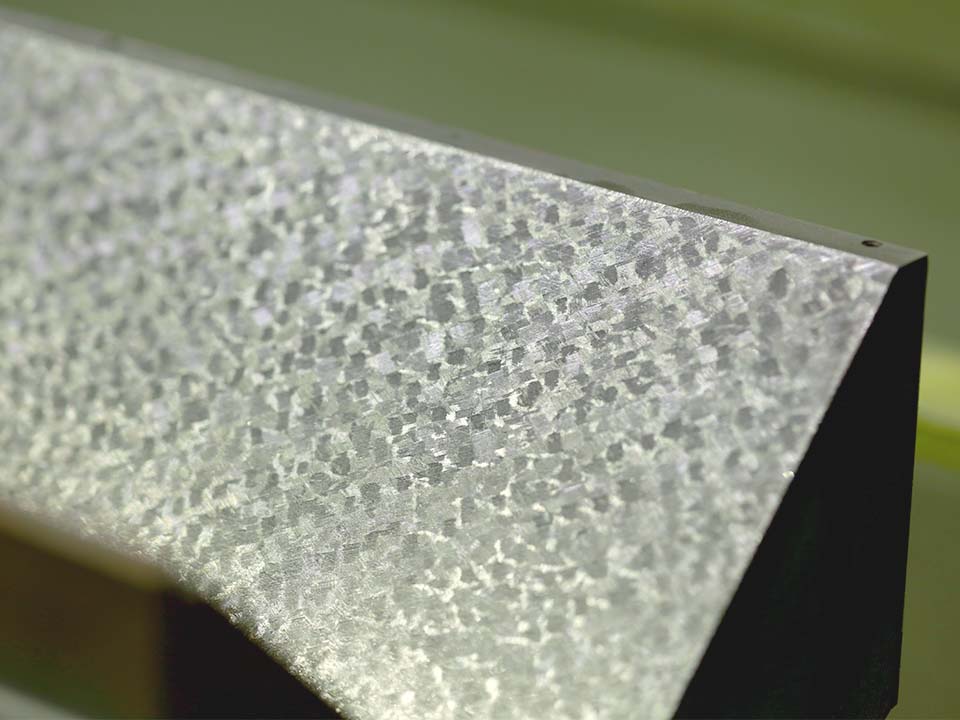
【物と物が接する部分】
ベッドとコラム、ヘッドとスピンドル、ボールねじブラケットと取付け面など、物と物が接する重要な部分にはきさげを施します。
それは一言で言えば、「ストレスをなくす」ということです。
例えば、【図1】のように平面が出ていないもの同士でも、ボルト等で締め付けて強制的に面と面を合わせることはできます。しかし、物体には常に元に戻ろうとする力が働いており、これが「ストレス」となっています。長い期間ではこのストレスが精度悪化の要因となります。
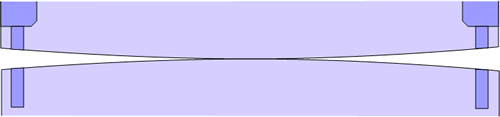
【図2】のように、合わせ面にきさげをかけ平面をきちんと出せば、面と面を合わせる際にはぴったりと合いストレスもなく長期的に安定します。
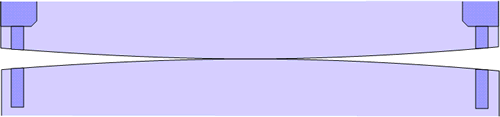
さらに、取付け面にある傾向をつけておくということも、きさげの重要な目的です。
ここでは立形マシニングセンタのコラム取り付けを例にとって説明します。【図3】はコラム取付け面をまっすぐに加工した場合をあらわしています。
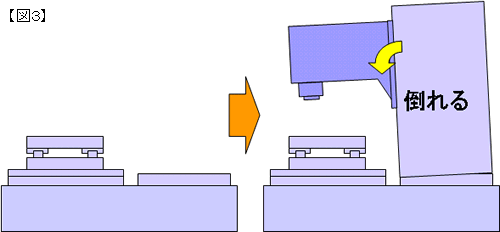
【摺動する部分】
テーブル、コラム、ヘッドなどが移動する摺動面の精度(真直度や直角度など)は機械精度の重要な要素です。摺動面でやっかいなのが、その上をモノが移動するということです。よたよたしないで、まっすぐに移動することが求められますし、移動すれば重心の変化が生じたりします。
【図5】は機械加工でまっすぐに仕上げられた摺動面です。この上をテーブルが移動した場合、ストロークの両端部分でダレてしまいます。中央部の精度は良くても、両端部の精度は落ちてしまいます。
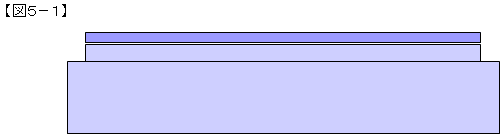
【図6】はきさげによって摺動面にある傾向をつけた場合をあらわしています。たとえば、わずかに(機械の大きさや仕様によっても異なりますが、数μmほど)中央部を低くしたカーブをつくります。こうすることで、その上にテーブルが載って移動したときには両端部でもダレずにまっすぐ動かすことができるのです。ここでは垂直面内での説明をしましたが、もちろん水平面内でも同様のことが言えます。
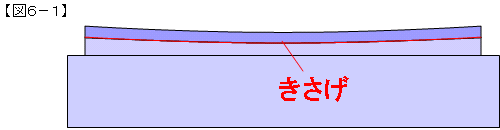
また、きさげした面が直接摺動面になる場合は微小なポケットが油たまりとなり、摺動面の潤滑と保護に役立っています。
ガイドレールの取り付け方法の違い
すべり方式のガイドレールを例にとって、一般的な方式と三井精機の方式の違いを説明します。
【図7】は鋳物の表面に焼入れ処理を行い、硬度を確保してからベッドウェイグラインダーで研削加工し摺動面をつくります。精度は一般的なものであり、表面硬度も高くないため耐久性も劣ります。摺動面が破損した場合も修復が困難です。
【図8】は三井精機が行っている方式です。鋳物のガイドレール取り付け面をきさげ加工で真直度等を出し鋼材を焼入れ研磨したガイドレールを鋳物面の裏側からボルトで固定します。
こうすることで初期精度はもちろん、長期的にも安定した精度を保ちます。また、ガイドレールも充分な硬度を持っているため耐久性も充分です。万が一、ガイドレールが破損した場合も交換が容易です。
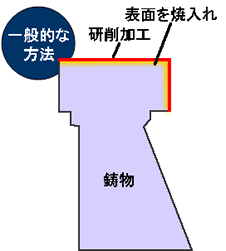
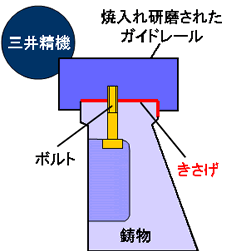
「きさげ」のお話〈3〉
きさげの工程 ~加工-測定を繰り返して精度を追い込む~
「きさげ」のお話〈2〉で説明した摺動面の加工を例にとって、きさげの工程を説明します。
- オートコリメータで加工面の状態を確認します。【図1】
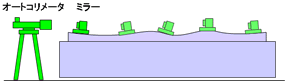
- ①で確認した測定値に基づいて、出っ張っている部分を荒取りしていきます。【図2】
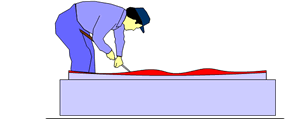
- オートコリメータで加工面の状態を測定し、目的通りのカーブに加工されているかの確認を行います。【図3】
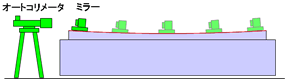
- 目的通りのカーブになるまで、きさげ-測定を繰り返していきます。【図4】
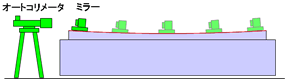
このように、きさげ加工は加工-測定を繰り返しながら精度を高めていく、非常に手間がかかる工程です。
しかし、それだからこそ、きさげ加工は機械加工では得られない高い精度を実現することができるのです。
真直度を測る ~オートコリメータについて~
オートコリメータは微小な角度を測定する装置で、【図5】のような構造をしています。
光源から出た光は対物レンズで平行光となり、ミラーで反射され戻ってきた光が接眼レンズで像を結びます。
ミラーの角度がずれれば戻ってくる光はそれに応じてずれるため、像のずれを測ればミラーの角度がわかるというわけです。
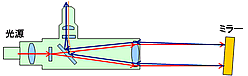
角度は1秒(=1/3,600度)以下という単位で読み取ることができます。
摺動面に置いたミラーを一定間隔で移動し、そのポイント、ポイントでの角度をプロットしていくことで摺動面の真直度を測ることができます。【図6】

きさげにもランクがある ~“あたり”について~
面と面の接触具合は、きさげのきめ細かさによって決まります。「あたり」というのは摺り合わせした後に1インチ四方(「一坪」とも言います)にどれだけの接触部分があるかを表します。「坪あたり10個」とか「坪あたり20個」などと言います。当然、あたりの数が多ければ多いほど面と面の接触具合が良くなり、高精度になります。
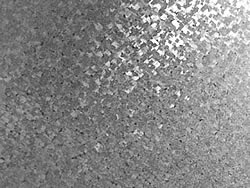
技能・経験が高度に融合した匠の技
一人前のきさげ職人になるには長い年月がかかります。卓越した職人はどれくらい加減すれば1μmの除去量になるのかを体で覚えています。
摺動面に置いたミラーを一定間隔で移動し、そのポイント、ポイントでの角度をプロットこれほど微妙な作業になるため、温度変化は大敵です。鉄は1℃の温度変化で1mあたり約0.01mm伸び縮みしますので、わずかな温度差があっても精度を出すことができません。昨日仕上げが終わったのに今日測定してみたら精度が出ていなかった・・・などということになると、いつまでたっても機械が完成しません。三井精機が一定温度の環境化でモノづくりにこだわるのは、このような理由があるからです。
きさげ面の微妙な模様はきさげ職人によって違うため、きさげ面を見ただけで、誰がきさげを行ったのかがわかるほどです。
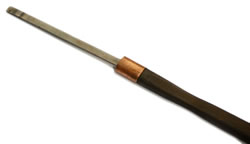
柄の部分が磨り減って凹状になっている
また、「きさげ」(工具)の刃物部分は使うと磨耗してきます。そうなると研ぐ必要がありますが、これはきさげ職人自らが行います。研ぎ方は荒取りか、仕上げかによって違いますし、人によっても千差万別です。その人が最もやりやすい形状や角度に研ぎます。きさげを研げるようになるにも、やはり長い年月がかかります。